Summary
- During the pandemic of 2020, I joined the medical team in support of COVID-19 rapid-test manufacturing, specifically, the kitting operation.
- Charged with implementing a kitting and packaging process, we started with a manual operation producing thousands of units per week and scaled to a semi-automated process producing over 1M units per week.
- Our solution was a success, hitting 95% of our production target in the first week of operation.
- The project yielded experience comprising all aspects of process development, from concept development and scale testing to vendor identification, capital requisitions, purchase, installation, integration, qualification, documentation, training, continuous improvement, and hand-off.
Background
2020 was an interesting year for most of us. For me it meant urgently redeploying from aerospace composite manufacturing to medical device manufacturing when the company where I worked won a contract to manufacture COVID-19 rapid tests and the demand for tests was exploding.
When I joined the project, teams of operators were assembling tests with hand tools in a small clean room producing about 10k tests per week. In order to meet the growing needs of the US rapid test market, the customer would be increasing production targets week over week and within months we would be expected to ship over 1M tests each week.
Scaling was urgently needed.
I was assigned to a small team consisting of myself, a project engineer, quality engineer, and a manufacturing engineer. We were instructed to develop and deploy a kitting and packaging operation, the last major step in the process, where all components come together to complete a shippable test kit. We had less than six months to design, implement, and qualify the operation and, in addition, we would need to support the existing operation to continue shipping in the meantime.
Manual Kitting
Our initial effort was invested in solidifying the manual kitting process. We opted for a modular kitting line consisting of a row of work tables where operators would stand as components were fed from the back of the tables to be carefully counted and placed into each kit box before passing down the line. At the end of the line a packing operator would place kits into their shipping boxes and then finally stack shippers on a pallet to be wrapped for shipment.
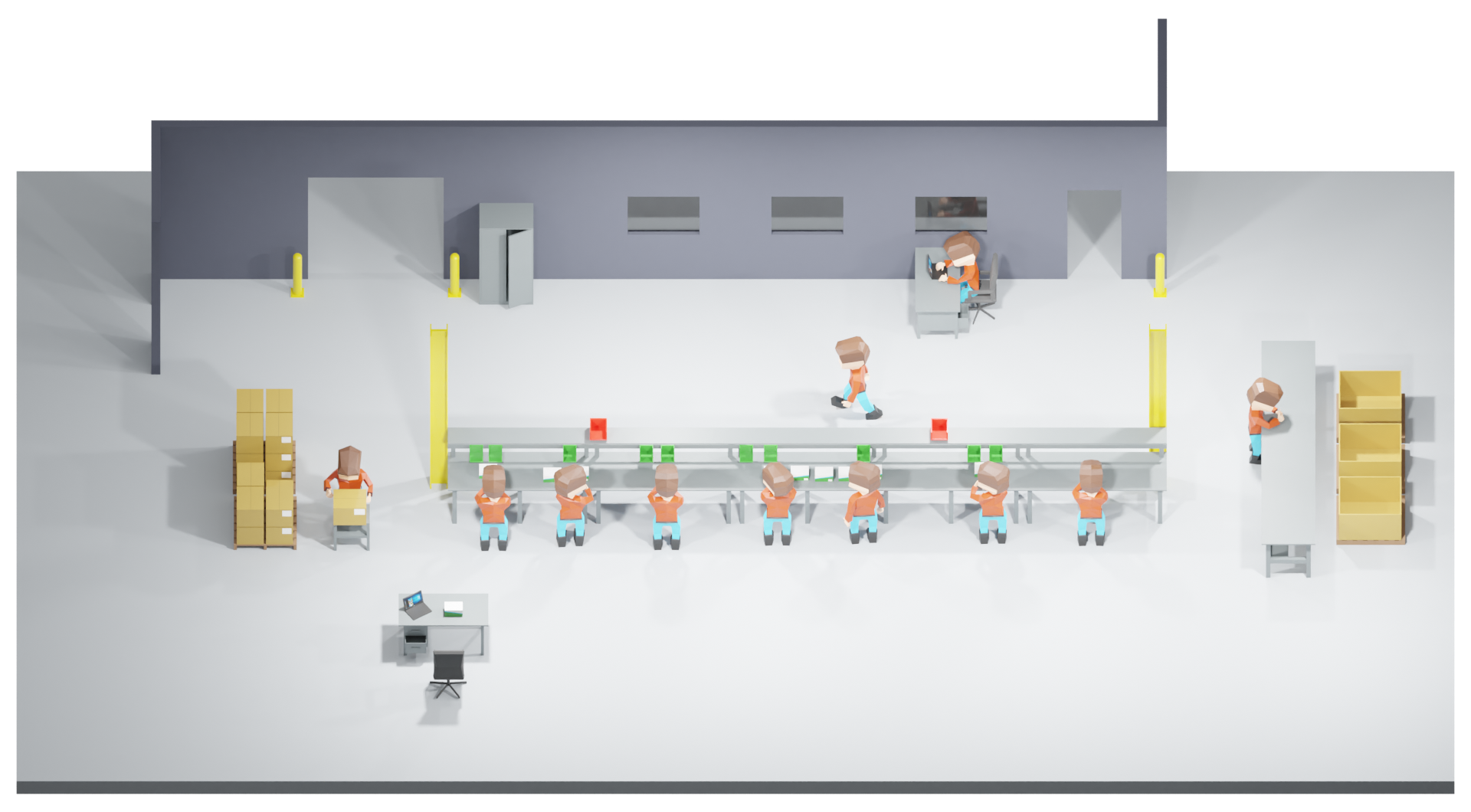
We planned our layout leaving room for additional lines, preparing to duplicate the process to grow our capacity when the demand required.
'Growing' a process in this way is distinct from 'scaling' because duplication yields no cost savings or efficiency improvements since operating costs are also duplicated. To scale a process, producing additional output from the same or fewer inputs, requires looking to lean principles to remove bottlenecks, increase uptime, and reduce waste and to automation to standardize pace and reduce variation.
Continuous Improvement
Manual processes are inherently high in variation often in a large part, due to the humans in the loop. Unlike machines, human operators are subject to fatigue, injury, illness, differences in training and language abilities, not to mention motivation or mood. The result of this myriad of 'soft' factors, is that productivity is highly variable and can be difficult to predict. Nonetheless, lean tools work well for identifying and eliminating bottlenecks in manual processes.
For example in a linear process like this one, significant downtime can be attributed to running out of a single component. In our case this was discovered when a time study of each kitting step revealed significant time spent waiting for components to be refilled. We addressed this issue by adding a material runner role, an individual whose sole responsibility was to keep each station stocked with components. The role added labor, but resulted a net increase the total uptime and output of the line with respect to total labor costs.
Once uptime issues were addressed, we turned our attention to making product flow smoothly. With an analysis of cycle times we discovered that each component required a different amount of time to place it in the kit and that overall, as the kit become more and more full, the time to place the next successive component increased. We were able to address these imbalances by shuffling the workload between operators such that the average amount of time that each kit spent at a given station was roughly the same.
Adding Automation
There comes a point in most processes improvement where continuous improvements have yielded the majority of the low-hanging-fruit, and additional improvements in productivity require more and more significant investment.
One trap I've observed in process development is the urge to automate too early. It is important to have a good understanding of the critical inputs and outputs of a process as well as identified primary bottlenecks and causes of variation before looking to automation. Nothing is more wasteful and counterproductive than spending time and money automating a step of the process that can actually be eliminated completely. In fact, according to Elon Musk, automation should be the last step one takes when improving a process.
We leaned heavily on outside vendors to educate us on packaging approaches and technologies. I was surprised, and a little disappointed to realize that designing processes at this scale and pace is more about locating, assessing, selecting off-the-shelf equipment and fitting the pieces together than it is about designing a comprehensive solution for the whole line. We spent a lot of time integrating, that is, figuring out how to fit machines together either mechanically with conveyors or electronically so that stopping one machine would signal or stop another, for example. We designed and fabricated a range of custom brackets, fixtures, and jigs, in the machine shop to bind everything together and tailor the off-the-shelf machines to the components and boxes they would need to operate on.
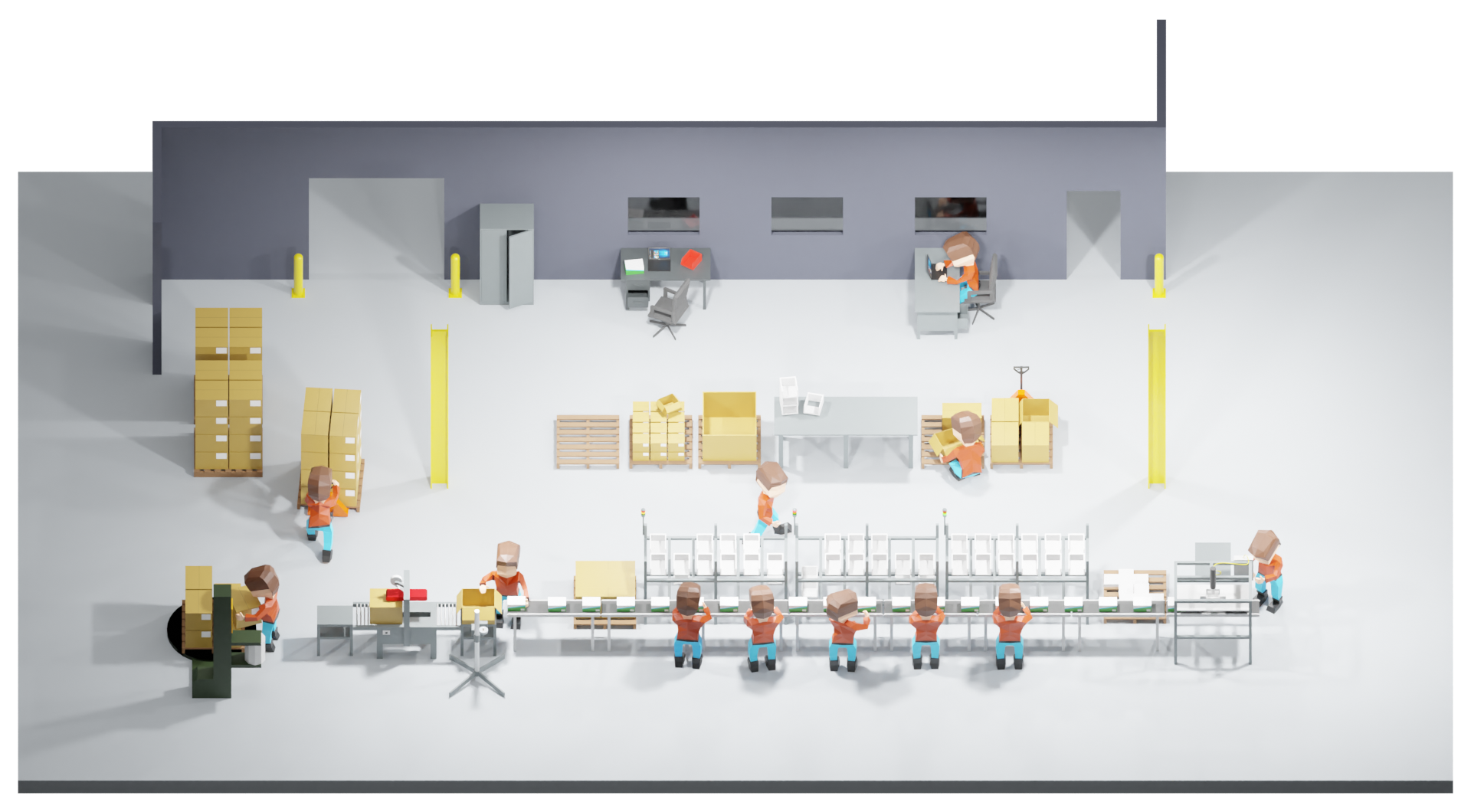
This semi-automated, second iteration of the line ended up being a combination of automated, semi-automated, and manual steps. Kit boxes were folded and glued by a machine and placed on a conveyor. The conveyor would carry the kit boxes past humans operators who would pick and place components into the boxes as they moved by. A human would fold each box closed but a machine would seal, label, weigh check, and count each kit before it was packed into a shipping box by a human. Yet another human operator would build pallets of boxes but a machine would automatically wrap and strap the stacked pallet for shipment.
We were ultimately pleased when the new process managed 95% of its' production target in the first week of operation and exceeded the target the week thereafter. Operator feedback was mostly positive as well, with several individuals even asking that the pace of the conveyor lines be increased!
Quality Control
The difficulty of affecting quality in a high-volume process is statistics. Given enough opportunities even unlikely events occur with near certainty. Six Sigma offers a set of statistical methods for quantifying a processes capability against a set of requirements and can pinpoint specific causes of variation and defect.
A common kit defect in this operation was most often an incorrect quantity of components included in the kit. For the sake of the end user, it was critical that the correct number of components ended up in the final package because a missing test would mean an upset patient, a potentially undiagnosed case, a waste of materials, etc. We focused our corrective actions and controls on solutions like weigh-counting components and check-weighing final packages. In addition, a rigorous statistical sampling plan was implemented to cover the outgoing product and provide feedback on quality.
Future State
The new process essentially doubled the capacity of the manual operation without any additional labor. With enough physical space for two copies of the semi-automated line, we would be able to support volumes up to about 2.5M units per week, which from projections from our management team would meet demand for several more months of growth.
The success of the semi-automated process painted the picture of a future state that would pack the kit and shipping boxes automatically as well. Unfortunately for my resume but fortunately for the world, we never got an opportunity to move past the design phase for a fully automated operation. Almost one year after I joined the project, COVID-19 cases finally began to subside and the bottom dropped out of the rapid-test market.
Thank you for reading.
Key Lessons
Last is first
Working on the last step in a process exposes you to all the escaped quality issues of upstream work centers. This effect is both challenging and interesting in that you are forced to become familiar with the operation of your supplier processes which and deepens your understanding of the value stream as a whole. This is actually a technique used in lean where when first beginning to observe a new value stream one first walks the process in reverse from the last step to the first.
The difference between unlikely and certain is opportunity
Thanks to statistics, at high product volumes, even statistically rare phenomenon will occur. Even a very small chance for a defect or failure to present become very likely given millions of opportunities to do so. Assess your process capability against specification limits, and update your PFMEA and control plans accordingly.
Humans are amazingly problematic
Humans are amazing and problematic (amazingly problematic?). Human dexterity is highly evolved and it is very difficult to replicate even parts of what we do instinctively with our hands with a machine. On the other hand, humans don't come close to matching the endurance and reliability of a machine. Together you can build a robust processes by correctly assessing and assigning tasks to humans or to machines based on their unique strengths and weaknesses.
Leave plenty of room
Automation requires floor space! When laying out automated equipment it's easy to locate things close together in CAD. However, once the flow of materials is considered, additional spacing needs to be left for materials to move in and out, operators to move around, technicians to access panels and controls, and the floor space requirement explodes. I'd estimate that converting a manual process to an automated one increases the footprint by at least 4x.